Tom, the plumber, as opposed to Tom, the neighbor, was out at the house two weeks ago. We wanted him to look at a couple of things and give us a quote on installing a gas line to the fireplace, one that will supply fuel for the gas stove. After showing him around the place I asked him to reroute a vent from the sink. The original plumber routed it straight up the wall and thru the roof. I'm not sure why he didn't tie it into the main vent stack, but I didn't like the extra breech in the roof... one more spot to potentially leak. Figured that it was a good time to make the change since the walls were open. Tom said it was an easy job...
But, we had to schedule the job to be completed before Caren and I could insulate and panel the walls. Tom squeezed it in last Friday. On Saturday we were paneling the wall...
This is what we started out Saturday morning with... The black PVC piping is the rerouted vent from the sink. It used to go straight up thru the roof just to the left of the kitchen window. It is now tied into the main vent stack so that, once we redo the roof next spring, we will only have on vent breech instead of two. Notice all the nail guards over the wiring and plumbing? More on that in a bit...
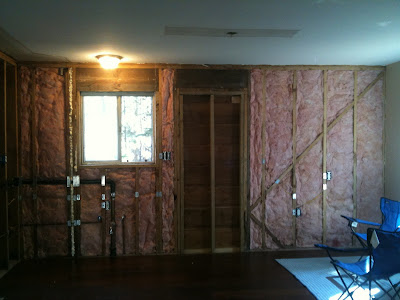
All insulated, except for where the door will be. The door should arrive next Saturday. Once it is in place the wall will be completely sealed... finally. It is amazing what just this little bit of insulation did to keep the place warmer on Saturday evening. Who'da thunk a bunch of pink fiberglass could do such a good job? Wish we could have fit more into the walls, but 2x4 framing will only allow for R13 rated fiberglass. Spray foam or rigid insulation would have given us a higher R value, but would not have been cost effective given that the rest of the walls aren't insulated with any higher value stuff.
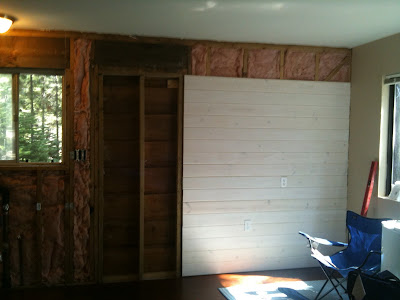
Part way into the paneling job... Caren and I both like the look of whitewashed pine paneling for the country kitchen/cabin feel. We ordered 1x6 tongue and groove from California Hardwood Producers, the same place that provided the flooring. Caren and Kelby spent a few hours white washing it two weeks ago. They mixed flat white ceiling paint with water in a 1:7 ratio to thin the paint down and applied a single coat. The result is an aged look that allows the grain of the wood to show thru. Basically, the boards look like they were painted years ago and have seen a little weather.
One of my little joys while doing the install was placing the outlet covers... something about a finishing touch even tho we are nowhere near finished. But, the outlet cutouts cause me problems to no end. I use present tense because I'm sure that they still cause me problems and will continue to do so in the future. For some reason I just can't seem to get the cuts right when making them, whether in drywall or paneling. I'm always off one way or another by just enough so that the cover won't quite hide my cut. The first outlet I came to took three boards and quite a little bit of cussing before I got it right (fortunately I could cut out the mistake and save the boards for later use). After the first one was done I developed a system that worked for all the rest of the outlets until the last one... one for which Caren had a good laugh at my expense.
Paneling job complete with enough time to install the frame work for the 1921 Detroit Jewel gas range that will go in the kitchen.
The posts, beam, and mantel work is very similar to that for the fireplace with a few exceptions... First, the posts and beam are from the wood salvaged from the Corning barn. Second, the mantle (really just a shelf) is from our neighbor's back yard, the remants of some mill work he completed for a client. It was cut using a chainsaw mill so has some really rough saw marks that Caren and I decided to leave in. Third, the wood definitely took the stain different than the fireplace mantel. It is more of a golden brown than the red brown of the mantel. Caren is not entirely happy with it, so we may be applying a red stain to it in an attempt to better match the fireplace.
The plywood up the center of the wall was designed to be a cost savings. Turns out it wasn't... Between the posts described above will be ledge stone and corrugated metal. No need to place the more expensive pine paneling if it is just going to be covered, right? We cut the paneling to fit the plywood, installed it, and made a quick trip to the DIY store... it really is called DIY... to pick up the plywood. They didn't have any full sheets of 3/4 inch, only half sheets. A full sheet of CDX grade 3/4 inch ply should run around $20. The half sheets that they had were $22 each. If I'm doing the math correctly, that is $24 just to cut a 4x8 sheet into two 4x4 sheets. I balked... but, Meeks, the local lumber yard, is closed on Sundays, and I fell into the just git'r done trap that I struggle with and ended up paying $44 for two half sheets. The pine paneling would have been about $52 to cover the same area. Big Savings!
Remember those nail guards in the first pic? I hit one with a screw while installing the plywood and nearly ruined Tom's work on the DWV system... fortunately the guard did its job and protected the pipe. Whew!
We also installed new valves on the sink supply lines. The cold water supply valve had a fitting for the water line to a refrigerator. We didn't need it, and couldn't turn the water on without somehow closing that line off, so... and of course, the hot water valve has to match the cold water valve. Valves are inexpensive.
Stove framework installed... We had Tom, the plumber, move the heat vent on the floor to its current position. Previously, it had been in the middle of the kitchen floor... don't ask me why. It would have been an easy job for me but involved crawling around under the house. Tom was going to be down there anyway so I thought I'd let him do the work...
Included this pic because, if one looks carefully, one can see the gas stub coming thru the wall just to the left of the left hand post. That's the one that we asked Tom to install before I got him sidetracked with DWV talk. Anyways, he finished the gas line too. The real reason that I included this pic though is because Caren sealed the stonework on the fireplace hearth before we left on Sunday. How cool does the finished product look?
So, we got the wall buttoned up in time for the snow... as long as we get the door installed in the next two or three weeks, but we still have to repair the bear damaged insulation under the house. Now, I'm learning what it means to be a general contractor, what with scheduling labor and all... Can't do the insulation next weekend because we have the floor nailer rented from the flooring place and need to finish the flooring in the bedrooms while we have it (yes, the rest of the flooring was delivered last week). Can't do the insulation the following week because Kelby won't be around to help with the install, and Caren isn't about to crawl under the house with me. Maybe, just maybe, I can get Alex or Zach to help...